空气热交换器和热能回收系统为美国印刷厂家的机械设备节能
位于威斯康星州的一家使用柔印设备的印刷商正面临着印刷厂的空气平衡问题。
能源回收
问题包括劣质空气状况有关的汇票与能源账单。与使用传统燃气补充装置简易处理空气不足问题相比,采用蒙特空气到空气热交换器来采集印刷机废气流中的热能效果更佳。
印刷产业采用不同的技术来生产各种印刷材料,如杂志和产品标签。从平版印刷、柔版印刷到网版印刷,这些各不相同的印刷工艺面临着一些共同的生产及环境挑战,其中包括能源合理利用、良好室内空气质量维护,以及设施内温/湿度的全年管理。
位于威斯康星州印刷厂内的卷筒纸印刷机需要大约23,000立方英尺/分钟(cfm)的空气来干燥印刷材料上的油墨。印刷机吸附了来自印刷厂的空气,其内部电热器将温度加热至160℉,并排出机外。这些损失的热能本可以轻松地得到采集,用于促进生产和增长利润。
蒙特热交换器
热能回收技术(如:空气到空气热交换器)早已应用于印刷产业,通过回收原本损失的热能来改善整体生产性能。使用蒙特热能回收系统为威斯康星的印刷厂带来了诸多益处。最重要的是,该系统帮助印刷厂摆脱了负压问题。印刷厂无需燃气加热器来保持厂内温度,由此降低了耗气量和维护成本。
热能节约的主要原因在于印刷厂的电热器无需频繁地操作。在一个特别的冬日里,热回收系统将外部空气从32℉加温至98℉,并直接将预先准备好的空气供应至印刷机。大部分外部空气的加热需要成本极高的电力。
年度热能节约金额逾80000美元,体现出了良好的经济效益。这同样是考虑环境效益和资源保护所采取的一项负责任的措施。
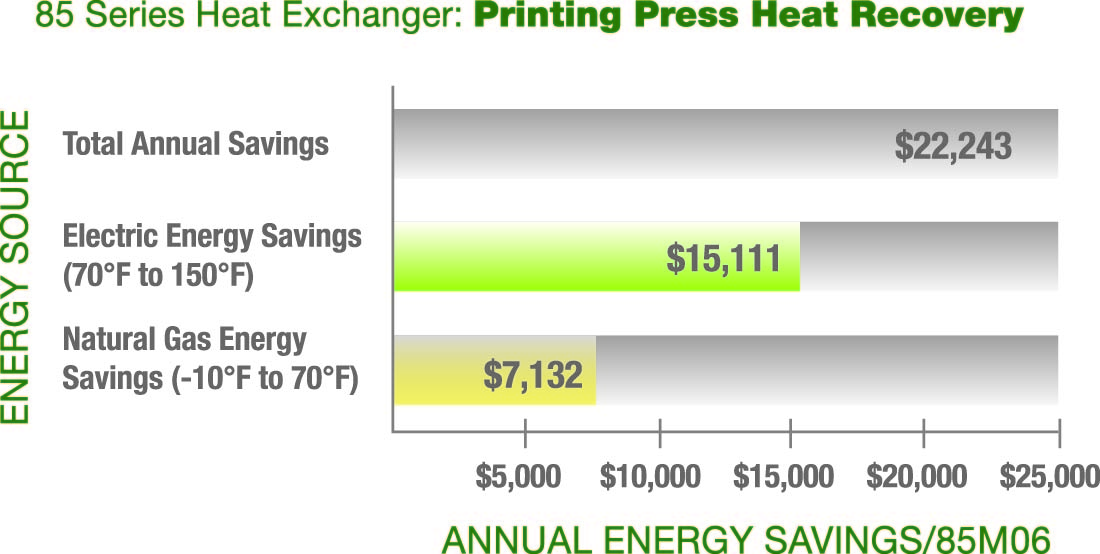
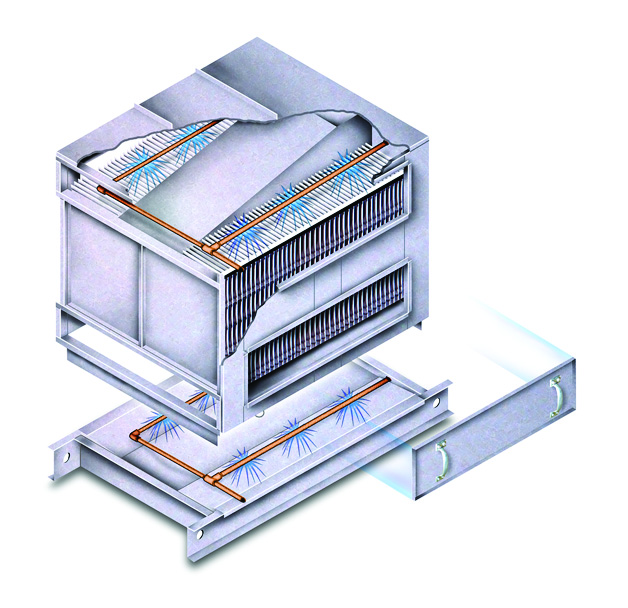