
Tyson solve condensation problems with dehumidification
Munters Desiccant Dehumidification equipment is used to control condensation formation in overhead areas while reducing energy costs by 35%.
The Problem
Tyson foods Arkansas, is the worlds largest processor and marketer of chicken, beef, and pork products. The company produces a wide variety of protein-based and prepared food products and is the recognised market leader in the retail and foodservice markets it serves. Tyson provides products and service to customers throughout the United States and more than 80 countries.
At Tyson's Arkansas plant 200,000 birds are processed per day. The production staff at the plant were spending a significant amount of time removing condensation that was forming on the overhead pipes and ceilings in the proximity of the bird chiller within the evisceration area. All condensation needed to be removed after sanitation and prior to the start of processing. "We were hanging plastic everyday over our chiller. The air temperature difference in this area was causing the ceiling to sweat," says Mike Hanson, plant manager. "We employed 2 people per shift to mop condensation around the chiller area."
In an attempt to eliminate condensation, fans were added to increase the air-flow in the evisceration area. This often brings in air at higher humidity levels, adding moisture and creating airflow imbalances that can increase condensation formation. Condensation may also be found in other areas of the plant due to the changing airflow patterns. Munters were contacted to design and manufacture a condensation control system that would eliminate the overhead condensation in this area.
The Solution
The addition of louvers and fans in various locations had changed the airflow patterns throughout the processing areas. An airflow test and balance was conducted to determine the existing airflow patterns and the corrective actions required to achieve proper airflows. In general, air should flow from further processing to evisceration and be exhausted from the pick scald area.
After analyzing the test and balance report a 37,378 m3/hr (22,000 CFM) Condensation Control system was selected. The system was equipped with PowerPurge™, Munters patented energy recovery system. Using PowerPurge resulted in energy savings of approximately 35% over a conventional desiccant systems.
Within hours of starting the Munters system up the condensation began to disappear. "Since installing the dehumidification equipment we have not had to hang plastic or have the 2 people per shift to control the condensation. We are not having to dry the ceilings in the morning following sanitation," says Mr. Hanson. "So far we are very pleased with the results and will use this technology in the future to help eliminate condensation."
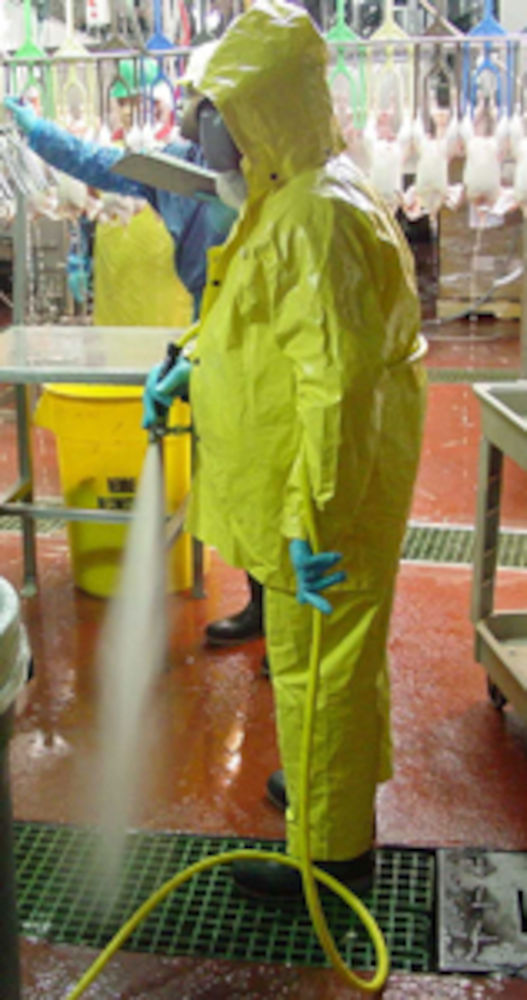
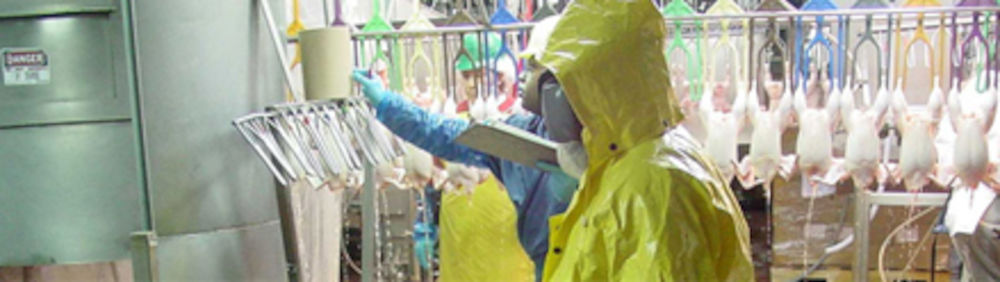