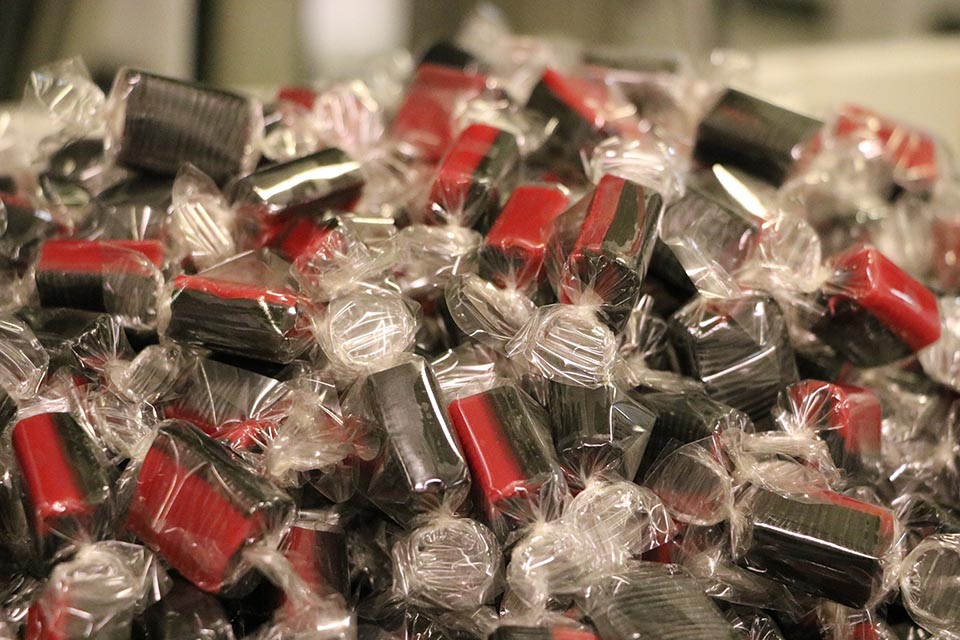
Packing of fudge and toffee products
The story of Kolafabriken in Bräkne-Hoby in Sweden started back in 1993, when the company took over some discarded production machinery from a caramel factory. Kolafabriken developed their own recipes for various toffee products and became the first Swedish industrial manufacturer of fudge products. Today a number of fudge and toffee products are produced to wholesalers, retail trade and private label production.
Sensitive to humidity
Back in 2009 Kolafabriken moved to new production facilities, where a traditional ventilation system with a very high airflow was already installed.
Since production of fudge and toffee products is sensitive to high humidity, it soon became obvious that the ventilation system led excessive amounts of outdoor air - and thus humidity - into the production halls. The AHU plant was therefore downsized to a smaller air volume, but on warm summers days with high water content in the air, severe problems in parts of the production arose:
- The cutting of fudge products requires absolutely clean knives, but with too much moisture in the air, the product starts sticking to the blades. This results in unsharp cut edges on the products, compromising the plant's high quality standards.
- The packing process turned out to be the biggest problem though. Normally the products are being wrapped and packed either straight away or after maximum half a day of drying, but on summers days with a humidity often reaching 60% RH, the products could not be packed until after 2 days of drying, which blocked the further production and thereby limited the company’s earnings.
Dehumidification was the answer
Munters got involved in the problems and recommended a solution based on a Munters desiccant dehumidifier type MX² 80 and a redesign of the existing duct work. The dehumidifier was installed and connected to the existing, but now further downsized AHU system, adding a pre and post cooler to condition the supply air. Since Kolafabriken has access to steam as a cheap energy source, the dehumidifier is steam regenerated, reducing the energy costs used for rotor regeneration.
Approximately 6,500 m³ of conditioned and dry air is now introduced into the production rooms with a constant humidity of 40% RH around the year.
By reducing the humidity and keeping it stable regardsless of the outdoor conditions, Kolafabriken now enjoys a consistent production climate, ensuring that all production processes can run smoothly at any time of the year and without unplanned interruptions.
Production capacity has increased, product quality is high and consistent, and the need of cleaning the machinery systems due to sticky products is significantly reduced and can be fully planned.
All in all factors that secured a short pay back time of the investment, and Production Manager Magnus Knutsson can concentrate on developing new, exciting confectionery products.
CONTACT DETAILS
Find your nearest contact here
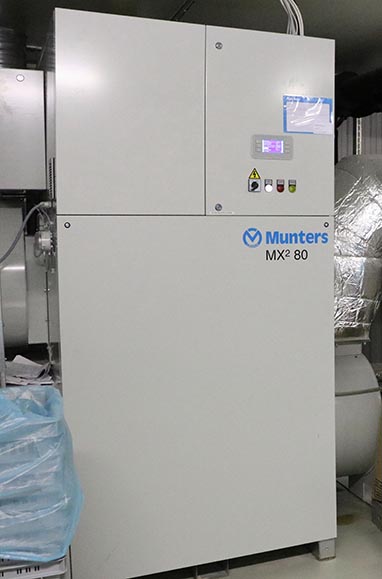
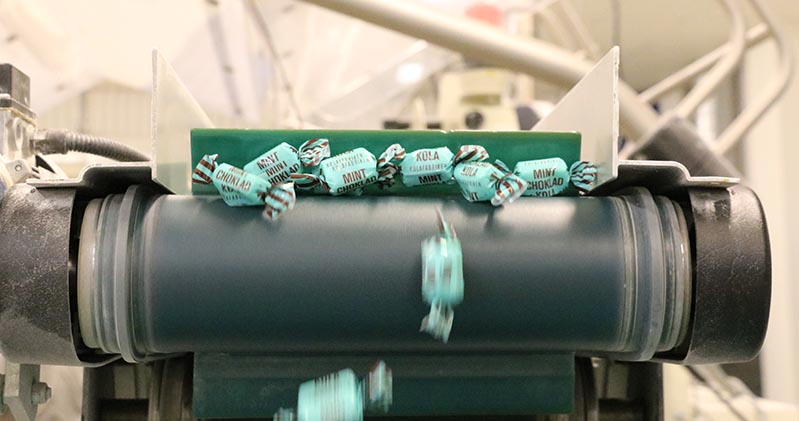